Challenges with Modern VFDs
Principal Phil Wentz discusses how VFDs have evolved over the years and the new unique challenges that have presented themselves to those who are specifying and designing them.
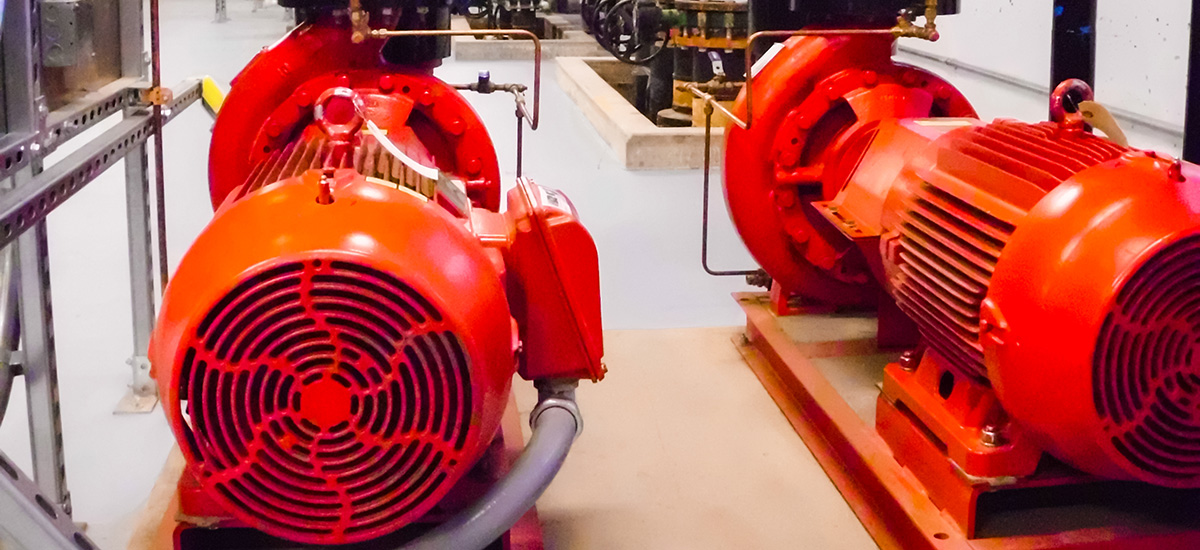
As VFDs have evolved over the years, new unique challenges have presented themselves to those who are specifying and designing them along with the motors they are controlling. These challenges have come about for a variety of reasons.
First, the motors being controlled years ago were overdesigned and less efficient than those we have today. VFDs did not have the technology to control as much so the motors had to be engineered more precisely and effectively. Because they were so overdesigned, the older motors were actually less prone to failure than today’s more efficient motors. Additionally, current VFDs have become smaller. Due to this reduction in size, there is less filtering applied inside of the drive due to costs and space constraints. There is a large propensity for rooftop mounting equipment, and VFDs are being placed farther away from the motors they’re controlling. Furthermore, when VFD technology was first introduced, it was much slower, especially when compared to the current Insulated Gate Bipolar Transistor (IGBT) technology engineers are familiar with today. This added speed can have an adverse effect on the longevity of the VFD controlled motor if not handled properly.
In order to solve the challenges presented by modern day VFDs, it is critical to understand what these challenges are, why they are more prevalent, and what can be done to counteract these negative side effects.
The Challenges
The primary issue that engineers are experiencing is bearing failure. Engineers are now seeing a reduced life in the bearing in the motors controlled by modern VFDs. The bearings are seen arcing from the bearing race to the bearing itself, creating a tracking within the bearing that leads to failure. This results in excess heat and grease running out, causing the bearing to ultimately fail.
A second issue to discuss is winding failure. This challenge stems from high voltages due to the large spikes from the VFD and the long lead lengths. The winding is created by the erosion of the insulation. Insulation breaks down within the windings of the motor and results in motor failure.
There is a Catch-22 situation at play here, however. Fixing some of these issues now opens another set of issues. Taking a step back, the entire reason a VFD is utilized is to increase efficiency of a system. At this point, if an engineer is adding a number of filters to make the VFD work, it may in fact be counterproductive. The engineer may be in better shape, in terms of efficiency, if he or she did not use a VFD at all. Individuals can get lazy and oversize their motor, and plan to just turn it down with their VFD to adjust it to where the design setpoint is. In this case, efficiency will actually be lost when compared to a situation if they would have just initially designed the motor for what it needs to do. Ultimately, as VFD technology has grown, individuals have relied a little too heavily on its functionality to fix problems that proper engineering would have solved.
Finally, feeder conductor failure is a growing issue. Just as the motor winding can break down, the motor feeders can break down due to the higher voltage running down the feeder. This voltage causes insulation pitting and access failure, resulting in issues.
Speed Considerations
As the drive operates, the inherent rise time of the transistor combined with the switching frequency causes voltage spikes that go down the line, creating differential mode voltage spikes. The drives did not always use to operate that fast. The faster impulses also lead to currents that no longer cancel each other out at high frequencies as the currents do at low frequencies such as 60 hertz (Hz).
These common mode currents that are developed are what create shaft currents and erode motor bearings as they return to the VFD through the grounding system. The higher the frequency of the IGBT in the VFDs, the smaller the capacitors and inductors they need to use. This IGBT speed increase has maximized the efficiency of the drive, but a higher carrier frequency will still reduce the efficiency of the drive while increasing the efficiency of the motor.
Motor Feeder Considerations
As the higher the pulses come, they travel down to the other end of the line and reflect back. They can either reflect back in phase or out of phase, and all of these effects are happening at much greater than 60 (Hz). Therefore, what typically would be 600 V is coming back at 1,200 V, twice the amplitude of the voltage that is anticipated. The voltage can also begin to “ring,” which can lead to even higher amplitudes. This is the additive nature of the situation being created, and this phenomenon ultimately breaks down the wire insulation. The wire could be rated at 600 V and is now seeing 1,200 V, causing failure.
The feeder capacitance is also a concern. The thicker the wire insulation and the greater the distance between the cables, the more capacitance can be built up between the cables within the conduit. That capacitance will now store some of the electrical energy until the insulation breaks down and pokes little pinholes through it. Basically, at high frequencies the capacitance becomes a short circuit to ground.
Some insulation is a uniform thickness and without voids. Other insulation is not sophisticated enough to handle these high-voltage and frequency scenarios. THHN wire, standard building wire, can sometimes be an issue. Alternatively, XHHW is usually thinner, thus a much better capacitance rating, as well as less prone to wick moisture. The insulation resistance after 12 weeks is drastically different in high frequency applications. This means the breakdown due to the high-voltage spikes discussed earlier is much less with the XHHW wire.
Motor Attributes
Over time, the motor impedances have decreased, with less resistance built into them in order to pass the most efficient standards. Motor impedance consists of inductance from the turnings of the windings as well as capacitance created between the winding insulation and the grounded motor frame. Larger motors tend to have significant inductance as well as capacitance. Smaller motors under roughly 10 hp often have more inductance than capacitance.
Part 30 states that the voltage peaks should not be subject to anything higher than 1,000 V and Part 31 says it cannot be higher than 1,600 V. Consequently, from a 480 V drive standpoint, it’s common for 12,00 V or greater to be observed, so specifying a Part 31 motor should be done for any 480 V application.
Voltage is built up in the motor itself, creating breakdown of the motor windings, so the increased capacitance is contributing to the failure of the motor itself. The increase in heat due to the high frequency stray voltage and related currents further deteriorate the insulation.
Measurement Methods
It is often less expensive and quicker to measure the issue before determining the solution. The phenomenon we are discussing can be measured, but not with typical electrical multimeters, which, even with the best available, are typically rated for under 1,000 volts and 200 kHz. Special high-voltage and high-frequency equipment must be used to fully measure and understand the issues.
The common mode current issues can be detected through a high-frequency (2k-10M Hz bandwidth) Rogowski coil. The flexible coil is wrapped around all three phase conductors but not the ground conductor. The coil is also connected to a high-frequency power analyzer or oscilloscope (greater than 40 MHz) to show the unbalances of stray currents which can lead to motor bearing failure.
An electrostatic discharge detector can also measure the high voltage discharge in the motor without touching the motor, providing a quick and simple check of motor health if performed on a routine basis.
Recommendations
In order to best counteract some of the concerns presented here, there are some standard recommendations. These recommendations increase in importance when the system voltage is above 300 volts and/or if the motor feeder is over 25 ft.
- Eliminate the VFD. Depending on the application, a properly sized motor with an across-the-line will save more energy at a reduced overall cost than an oversized motor with a VFD.
- Quality VFD. Engineers should use quality drives with some level of built-in filtering and controlled switching. This will lead to cleaner wave form. If the wave form is controlled, it does not have to be fixed as much.
- Quality TEFC motors. Motors should be built to Part 31 specifications and have properly filled voids and uniform windings and insulation. Lower quality non-uniform motors often generate imbalanced stray voltages and currents which result in bearing failure. Shaft grounding brushes do not fix this issue but can mask it. Total enclosed fan cooled (TEFC) motors minimize internal moisture which when heated leads to winding and insulation failure in open drip proof motors (ODP).
- VFD location. Shorter feeder lengths are recommended due to the reflective voltage. The general rule is that the less distance, the less chance there is for reflective waves to develop and create an issue. This also leads to less of a chance for there to be breakdown of insulation. Finally, the feeders of multiple drives should be isolated from one another so there is not interference.
- Proper grounding. Review of the grounding components is also a strong recommendation. With a focus shifting to inexpensive motors, some of the connection boxes are not grounded properly due to mechanical looseness and paint. Often, the flex connection back to the rest of the conduit is not properly done because there is not much room at the motor connections. The high-frequency currents must have a continuous path to get back to the drive, or it will find an often-dangerous path that will lead to failure.
- XHHW conductors. XHHW should be used for feeder conductors to motors to minimize feeder breakdown as well as reduce the capacitance and the voltage levels that can be created in the feeders. XHHW conductors should also be used whenever water may be present as in underground or some mechanical spaces as it has greater immunities to moisture.
- Optimized carrier frequency. It is best to look for the optimum fit between the noise generated by the motor (carrier too low, motor inefficient) and the too high (reduced efficiency in the drive itself). The typical carrier frequency that works for most HVAC applications is around 6 kHz.
- Most VFD installations, when following the above recommendations, do not have an issue and do not need further mitigation. On small motors, such as in the HVAC industry, providing mitigation on every motor when most do not have an issue can be cost-prohibitive. In critical applications or large motors, mitigation up front could be warranted. Either way, if you find that motors are not lasting as long or if there are intermittent issues with the power system, measure the system and determine the appropriate solution.
- Common mode choke. If the high-frequency common mode current measurement indicates a high imbalance current, a common mode choke is recommended. This is an inductive core presented around the phase conductors to absorb the common mode current. This current causes a large amount of bearing failures. By utilizing common mode choke, this failure can be mitigated effectively. Smaller motors under 10 hp often benefit from a different mode choke on each phase line as well.
- Risetime filter. If the measurements indicate high voltages, a dv/dt or risetime filter is the best choice. Often these are combined or integrated with a common mode filter for a complete solution.
Failures due to the use of modern, more sophisticated VFDs and efficient motors can be avoided with proper engineering. Utilizing some of the methods mentioned in this discussion should help keep motors running efficiently and for a longer period of time.
Phil Wentz, P.E.
Published April 6, 2018 in Engineered Systems
Phil Wentz, P.E., is a principal at McClure Engineering, a mechanical and electrical consulting engineering firm dedicated to the development of innovative solutions to unique engineering problems.