Is Your Operating Room Sweating This Summer?
There are a few tricks that the facilities staff can use to help keep the room open until the bigger problem can be addressed.
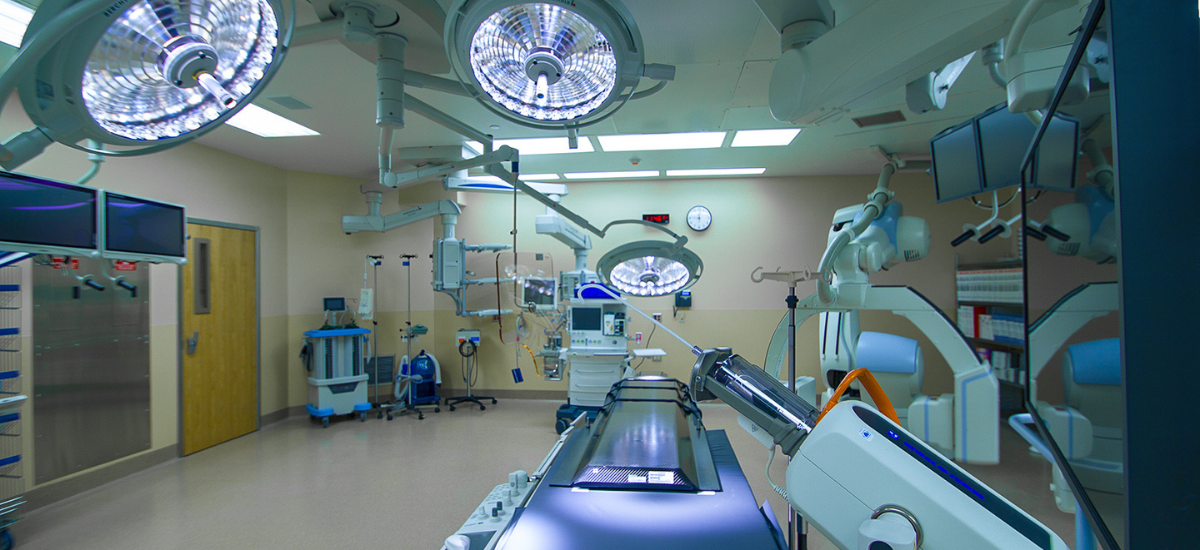
In the last few years, clinical staffs began recording the temperature and humidity levels in operating rooms throughout the year. As a result, many hospitals found that in the hot, humid months especially, it’s a struggle to meet the 60 percent maximum relative humidity limit (% RH) in their operating rooms (ORs). Previously, facilities did not monitor humidity levels for each OR all day throughout the year, and small lapses where a space went above the 60% RH threshold briefly went unnoticed. As staffs are paying more attention to the level in the room daily, these small blips are becoming a bigger nuisance and problem for hospital staffs.
While each state has its own requirements for temperature and humidity levels, 60% RH is commonly accepted as the maximum limit for the ORs. This maximum limit comes from both comfort and health concerns. When a space exceeds 60% RH, occupants may start to notice the humidity in the room due to the “sticky” feeling in the space. From an HVAC designer’s perspective, occupants are typically more comfortable at 75°F, 50% RH than they are at 72°F, 70% RH. The misconception that colder is always better often leads to humid spaces that doctors still complain are “too hot and uncomfortable.” In addition to the comfort concern, there is data to support that bacteria and fungi growth is accelerated when relative humidity of a space gets above 60% RH.
There are several reasons why the humidity level in the space may be creeping up over the limit. The first elements to consider are the original design of the space and the thermostat’s current setting. Just because the system can cool the OR down to 60°F, it doesn’t mean that it can maintain the humidity below 60% RH at this temperature. ORs have a lot of air blowing through them, which makes it relatively easy to cool the space down below the design temperature. Facility staff, as well as the clinical staff using the rooms, should be aware of what the room was designed for and not attempt to take it below that temperature. Our recommendation would be to make sure occupants can’t set the room temperature below the design. With automated controls, it’s easy to lock out a thermostat so it can’t be adjusted below a specific temperature.
Another important factor to understand is that the humidity sensors on the wall are not the most robust and accurate devices in the system. A good HVAC-grade sensor might be accurate to within a couple % RH for a few years at best. Inherently, the accuracy of these devices degrades over time. We have seen many facilities with a cheap humidity sensor that the staff bought at the local pharmacy hanging on the OR wall being used to chart room conditions for the clinical staff. Since these conditions in ORs are critical and being recorded for the state at facilities, it is important that the sensor which the facility staff is looking at on the controls system is the same one the clinical staff is seeing in the space and recording for their records. Furthermore, the higher quality sensors which would be part of the HVAC system are able to be calibrated, which staff should do annually. The first thing the facility’s staff should do when an alarm alerts for high humidity is take a sling psychrometer into the space to check the conditions and verify sensor accuracy. A faulty humidity sensor is probably the most common and simple problem to fix.
We’ve worked with several healthcare facilities and there is always differing opinions between departments on “What is an appropriate temperature for the OR?” Many of the states refer to ASHRAE 170, which asserts that the design temperature for an OR should be 68-75°F, 30-60% RH. In our experience, few doctors are satisfied with an OR at 68°F. Most medical professionals want lower temperatures in the mid-60s and some even prefer temperatures approaching the lower 60s. The reality is there are several facilities that are operating the ORs at 65°F and are having trouble maintaining humidity levels. Often the facility staffs are surprised to learn their space was designed for the ASHRAE guideline of 68°F and they didn’t even know they were taking the rooms outside of original design.
We encourage hospital staff to take an active role in the design, so that they have input on the design conditions for their ORs. If they are working with a design team to plan a new OR, owners should be asking the question (if the engineer isn’t already), about design conditions. Our next recommendation would be that if the hospital staff is requiring a minimum temperature in the OR of 65°F, 60% RH, the engineer should not be using that for their equipment design condition. Considering that at many facilities a condition of 65°F, 61% RH will result in a phone call to the facilities department, we need to leave some wiggle room in our designs. As a general rule, we use a couple degrees as our safety factor. For example, if the owner requests 65F, 60% on the low end, we design the equipment for 63°F, 60% RH. Typically, design engineers are using historical weather data based on 99.X% values, which means that every year there are always a handful of hours that are above the design conditions. One percent of the year equates to approximately 80 hours. This might be four hours in the afternoon for 20 days that are above design conditions! Considering there are always extremes in weather above the historical data and the reality that the HVAC equipment doesn’t typically get more efficient over time, owners should make sure their design engineers have included some safety factor.
So far, we’ve discussed several reasons why humidity levels in an OR might be rising over the limit as well as ways to prevent them. However, none of those are particularly helpful to the facility employee who has a problem and needs a quick fix. So, what are some tips for when an OR starts raining?
The initial reaction should be to turn up the temperature in the room! Relative humidity is dependent on temperature. More specifically, warmer air can hold more moisture. Without changing the amount of moisture in the air, simply heating the room a couple degrees will drop the relative humidity in the space. We have made this an automated response at some facilities. The building automation systems can be programmed to automatically reset the temperature when relative humidity starts to approach the limit.
The next step is to check the air handling units that serve the OR. It is important to make sure that the proper amount of outside air is being provided to the unit. This may mean cleaning/verifying flow stations or having a balancer check airflow. If too much outside air is being provided on a hot, humid day, the air handling unit may not be able to meet design. Additionally, if there are humidity problems, lower discharge air temperatures are good. If one can achieve colder discharge temperatures or colder chilled water, it will help alleviate the problem temporarily until the bigger problem can be solved. Also, condensate traps must be working properly. Traps not draining properly may be adding to moisture carryover issues, and they result in warm humid air bypassing the cooling coil and diluting the conditioned supply air. This same thing can be caused by leaks in the air handling unit’s casing after the cooling coil.
Lastly, if the temperature in the OR and the air handling units are meeting design, one should verify building pressures and look for building leaks. In a real-world example, there was a project a couple years ago that involved a few new ORs and we were experiencing capacity issues the first summer. All the HVAC equipment was performing as designed and we were delivering good dehumidified air to the space. After installing some data loggers in various locations in the room we were able to identify that the additional moisture was coming in from outside as one of the ORs was on an exterior wall. While small leaks in the building can be a problem regardless when it comes to critical spaces like an OR, they are amplified if the building is negative, sucking hot and humid air in from outside through the leaks. Since the project was constructed in several phases, there were adjustments at each phase that had to be made to the exhaust and outside air on the unit to make sure the surgery suite remained positive. We learned that this was not being completed and the surgery suite was significantly negative during a couple of the phases that summer causing our problem.
It is not uncommon for us to find HVAC systems serving an OR that cannot meet the performance required by the OR staff. There are many reasons why this might be occurring, but there are a few tricks that the facilities staff can use to help keep the room open until the bigger problem can be addressed.
Erik Reuther, P.E.
Published August 2, 2018 in Health Facilities Today
Eric Reuther, P.E. is a Principal & Mechanical Engineer at McClure Engineering.