Temporary HVAC for Construction Activities
The quality of your preparation determines the quality of your performance.
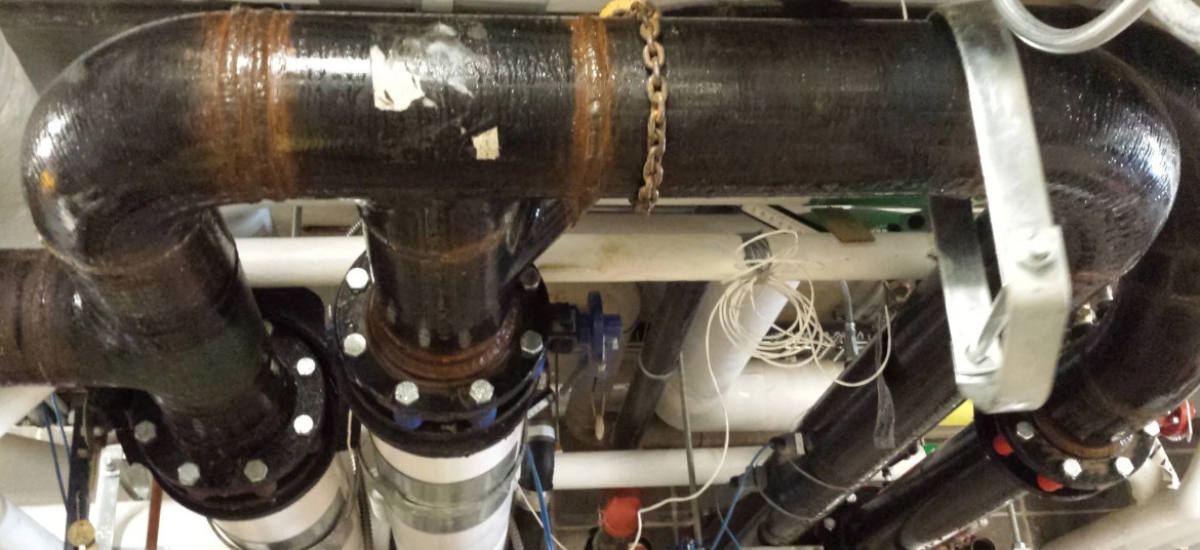
Mid-afternoon on day two of virtual kindergarten last year, the teacher asked my granddaughter, “Do you want to stop now?” She replied, “Yes, and I want to stop for tomorrow, too.” Sometimes, I think general contractors on my projects have this same approach to “temporary conditioning” of the building environment during construction. They push costs to subcontractors or avoid conditioning the building under construction as long and as far out as possible. Maybe the low-bid contractor is the one that excluded the biggest portion of this cost. Maybe we should find a better way to plan and account for the costs of temporary conditioning for the building environment during construction.
Figure 1: Gym temporary conditioning: A gymnasium being temporary conditioned by a combination of an exterior temporary HVAC unit and rental dehumidifiers
Often, the plan is for using the permanent HVAC system for building conditioning during construction. Doing this puts the permanent system at risk, causes concern for dirt in the system, and creates regard for lingering air quality issues after occupancy. This will require the mechanical subcontractor to get extended or special warranties for equipment. Some equipment manufacturers may not offer an adequate extended warranty for their equipment, which will require the installing contractor to carry this risk and expense. It’s a good idea for the architect and consulting engineer to include specification section 33 01 00 Extended Service Operation and Maintenance of Facilities in their project documents. Sheet Metal and Air Conditioning Contractors National Association (SMACNA) also discourages this practice. See the organization’s publication, “Temporary Uses (Early Start-Up) of HVAC Systems In Building Construction Projects – The Realities and Risks of Using Permanent HVAC Systems.”
So, why can’t we use the permanent HVAC equipment to condition the building during construction? This approach pushes a specific group of subcontractors to complete a significant amount of work ahead of a normal, reasonable schedule. Sometimes contractors just cannot get this work completed this far ahead of schedule.
Figure 2: A permanent rooftop unit with piping in progress.
Figure 3: A permanent rooftop unit with piping into the piping ‘doghouse.’
McClure Engineering has developed the following specification for contractors to follow when the permanent system is used for space conditioning during construction:
20 00 21 TEMPORARY FACILITIES
Temporary Conditioning of Air (Heating/Cooling)
- The permanent HVAC systems and machinery shall not be used for temporary heating or cooling during construction. Any devices required for temporary conditioning of the spaces shall be the responsibility of the general contractor.
- The respective contractor or subcontractor shall provide temporary conditioning to all areas affected by the scope of work. All spaces affected shall have no interruptions in any utility services including, HVAC, plumbing, etc. The contractor shall provide temporary piping, ductwork, and spot coolers/heaters as necessary to maintain the existing conditions of all spaces affected by the scope of work.
- If the contractor should request through a separate agreement with the owner to utilize the permanent systems or equipment for temporary space conditioning, the following minimum conditions shall be a part of that agreement:
- a) The return air system shall not be used as much as practical, and where it’s used shall be filtered at all air openings to units with temporary filters comprised of two layers of MERV-8, ¾-inch-thick, tactified, polyester media roll product, securely fastened to the return air opening of the rooftop unit or return duct plenum. Where indoor air-handling units are used, the return air ductwork shall be sealed and return air shall be through the return plenum access doors of the unit immediately upstream of the filter section.
- b) All safety devices shall be installed and operative.
- c) Temporary MERV-8 filters shall be installed in the filter section(s). These filters shall be removed and discarded at the end of the temporary period.
- d) At the end of the temporary period and before acceptance, all coils shall be chemically cleaned, and all supply air system(s), including ductwork, plenums, and air devices, shall be cleaned and return air system(s) activated all to the satisfaction of the architect/engineer.
- e) The contractor shall secure an extended factory warranty of the HVAC equipment for portion of temporary use, such that the owner retains a full two-year warranty upon receipt of substantial completion of the entire project or portions thereof where turned over to the owner for beneficial use.
There are two seasons of temporary conditioning: heating and drying (often referred to as cooling):
- Defining the temporary heating problem by construction tasks:
- Cement masonry units (CMU) block lay-up, 45°F (7.2°C) minimum;
- Tile setting, 45°F (7.2°C) minimum;
- Painting, 50°F (10°C) minimum;
- Drywall/taping, 55°F (12.8°C) minimum;
- Wood flooring, 60°F (15.6°C) minimum and 35% minimum RH; and
- Vinyl composition tile (VCT) installation, 65°F (18.3°C) minimum.
- Temporary wall and envelope closures may be acceptable for heating needs.
- A clean site is important for safety and for contaminant control.
Figure 4: A building envelope requiring heating during construction with temporary opening closures.
Concerns with Portable Heat:
- Fire hazard (safety);
- Burn hazard (safety);
- Lack of distribution (hot spots); and
- Carbon monoxide? (which is not supposed to be a problem, but it can occur if temporary equipment and space conditions are not closely monitored.)
System Risks to Temporary Heating:
- Flow failure;
- Freeze failure;
- Dirt in the HVAC system; and
- Loss of fluid (left a joint or valve open).
Keys to Successful Heating Using the Permanent System:
- Enclose the building – some temporary envelope closures are OK;
- All safeties are in place;
- Means of monitoring – modem or GSM;
- Wild coils are OK;
- Keep job site impeccably clean;
- Seal the return and exhaust ductwork;
- Extract welding fumes to the exterior;
- Crack the outside air damper to pressurize the building;
- Boilers on local control;
- Heating water pump(s) at 60 Hz;
- Startup strainers remain in place;
- AHU fans at 40 Hz;
- Filters in place – MERV-8 minimum;
- “Basic level” duct cleanliness; and
- Ducts covered to “intermediate level.”
Temporary Loads can Be Quite Different from Normal Operating Loads:
- 3.2 MMBtuh calculated operating load; and
- 0.7 MMBtuh calculated temporary load.
Figure 5: Example system conditions for temporary heating, identifying minimum controls, safeties, and operating conditions.
“The only difference between a problem and a solution is that people understand the solution.” — Charles F. Kettering
Defining the Drying (Cooling) Needs Problem:
- Painting – 95°F (35°C and 85% RH) maximum;
- CMU block lay-up – 90°F (32.2°C) maximum — 15 minute open time, 30 minute pot time;
Drywall/taping – 90°F (32.2°C) Maximum:
- @60°F and 85% RH – 38-hour dry time;
- @70°F and 50% RH – 17-hour dry time;
- @80°F and 20% RH – eight-hour dry time;
- VCT installation, 85°F (29.4°C) maximum;
- Tile setting, 70°F (21°C) maximum; and
- Maple gym flooring, 55°F to 75°F (13°C to 24°C) and 35%-50% relative humidity, wood floor materials should be acclimated in the room/gymnasium for at least three days before installation.
Drying (Cooling) Risks:
- Condensation on building surfaces;
- Condensation on pipe surfaces;
- Insulation incomplete;
- VAV reheat return bends;
- A focus on cooling instead of dehumidifying;
- Dirt in HVAC systems – especially with wet cooling coils; and
- Operating conditions must be controlled and monitored.
FIGURE 6: Condensate forming on VAV reheat coil. The cold air flowing over the reheat coil Cools the coil casing and condenses moisture out of the humid air during construction.
Keys to Successful Drying:
- Enclose the building – no temporary closures;
- All safeties in place;
- Means of monitoring – modem or GSM with auto dialer;
- Cooling coil under control (wild cooling coil OK only if reheat is controlled in HVAC systems);
- Keep job site impeccable and doors closed;
- Seal returns and exhaust ductwork;
- Extract welding fumes to the exterior;
- Crack the outside air damper to pressurize the building;
- Diffusers in place to prevent overcooled surfaces;
- Secondary pumps cannot overrun primary flow; and
- Cooling tower treatment in automatic control.
Cautions:
- Mold growth can occur in 48-72 hours; and
- Moisture remediation requires RH <30%.
Moving air (fans) is not the same as drying or dehumidifying, which is the goal and real benefit.
FIGURE 7: Opening the exterior door and using a fan to move air will not dehumidify the construction space.
FIGURE 8: Portable dehumidifiers are often used to condition the construction space for tasks such as taping and tile setting.
FIGURE 9: Example system conditions for temporary drying (cooling), identifying minimum controls, safeties, and operating conditions.
“You will only be remembered for two things; the problems you solve and the ones you create!” — Mike Murdock
Not to be confused with, “Unified Facilities Guide Specifications (UFGS) 01 57 20 Environmental Controls. Federal Facility Criteria: Department of Defense,” McClure Engineering has developed the following specification section for inclusion in the project front-end specifications for the general contractor to include the cost and risk of controlling the construction environment.
SECTION 01 57 20 MOISTURE SAFETY, TEMPORARY DEHUMIDIFICATION, AND CLIMATE CONTROL
- Required – The temporary climate control submittal schedule and moisture intrusion mitigation plan must be submitted with the project critical path schedule.
- Provide a complete list and product data sheets for the following:
- Dehumidification, and/or climate control equipment;
- Humidistat and/or thermostat control;
- Temporary air distribution, chilled water hose, gas piping, electrical cable, and accessories; and
- Temporary power and/or job site fuel requirements.
- Shop drawings, including:
- A moisture safety plan shall be provided that ensures the building area has no moisture intrusion during the construction process. Ensure the manufacturer’s installation requirements are met or meet the following installation conditions:
- CMU block lay-up, 45°F (7.2°C) minimum, 100°F (37.8°C) maximum;
- Tile setting, 45°F (7.2°C) minimum, 85°F (29.4°C), and 80% RH maximum;
- A moisture safety plan shall be provided that ensures the building area has no moisture intrusion during the construction process. Ensure the manufacturer’s installation requirements are met or meet the following installation conditions:
- Painting, 50°F (10°C) and 40% RH minimum, 85°F (29.4°C) and 70% RH maximum;
- Drywall/taping, 55°F (12.8°C) minimum, 95°F (35°C), and 80% RH maximum;
- Wood flooring, 60°F (15.6°C) and 35% RH minimum, 80°F (26.7°C), and 50% RH maximum;
- VCT installation, 65°F (18.3°C) minimum, 95°F (35°C), and 65% RH maximum; and
- LVT installation, 55°F (12.8°C) minimum, 85°F (29.4°C), and 65% RH maximum.
- Equipment layout plan indicating planned equipment location and approximate routing of air distribution, electrical cable, chilled water hose, and/or gas piping.
- A plan for staging and sequencing.
- Layout of enclosures and barricades.
- Layout of enclosures and barricades.
- Moisture intrusion events must be reported. Regular moisture reviews must be recorded. Use of moisture meter, Delmhorst BD-2100 or equivalent is recommended. Drywall is considered “wet” if moisture content >1% on a gypsum scale. Two-towel system for water/moisture cleanup is recommended.
- Significant moisture events and observations of mold growth require remediation action.
- Provide equipment manufactured specifically for temporary dehumidification, climate control, and drying when temperature or relative humidity cannot be maintained in ambient conditions as specified in this section or other sections of this specification.
- Acceptable temporary equipment providers include Polygon Group, Temp-Aire, Sunbelt Rentals, Aggreko, Munters, or equivalent.
- Temporary Climate Control Performance Criteria:
- Supply air quantities: 0.5 air changes per hour, minimum.
- Outdoor air (OA) quantity: 10% minimum or 20 cfm (cubic feet per minute) per person, minimum, whichever is greater.
- Filtration for OA: MERV 13 minimum.
- Return air opening filtration: MERV 8 minimum.
2.2 – Temporary Dehumidification Equipment
- When job site conditions are outside of the manufacturer’s recommended temperature and humidity requirements, provide temporary desiccant dehumidifiers with a single rotary desiccant wheel capable of fully automatic continuous operation. Desiccant dehumidifiers are required when dry bulb temperatures are expected to fall below 55°F and in all accelerated concrete drying applications.
- The minimum wheel depth shall be 8 inches.
- Dehumidification equipment shall utilize sufficient outside air to meet the aforementioned OA requirements. Indoor air shall not recirculate through dehumidification equipment without prior approval.
2.3 – Temporary Cooling or Refrigeration-Type Dehumidification Units
- Temporary cooling equipment shall be used if temperatures in the space exceed 80⁰F.
- When called for, provide temporary cooling units or refrigeration-type dehumidifiers with the following performance criteria:
- Equipment shall maintain temperatures below 80°F.
- Equipment shall provide air quantities to conform to the requirements of the temporary climate control system.
- Cooling equipment may be used to control humidity under the following conditions:
- Humidity is to be maintained at 50% maximum.
- Ambient dew point temperatures are expected to remain above 55° F dewpoint.
- Reheat coils are utilized to lower relative humidity in the airstream.
- Cooling units shall utilize sufficient outside air to meet the aforementioned OA requirements. Indoor air shall not recirculate through cooling equipment without prior approval.
2.4 – Temporary Heating Units
- Temporary heating equipment shall be used if temperatures in the space fall below 40⁰F.
- When called for, provide only electric or indirect-fired heating equipment.
- Heaters must be equipped with controls that will automatically turn the heater off if the airflow is interrupted or the internal temperature of the heater exceeds its design temperature or that of the supply duct.
- Heating units shall utilize sufficient outside air to meet the aforementioned OA requirements. Inside air shall not recirculate through heating equipment without prior approval.
2.5 – Temporary Ductwork and Air Distribution
- Provide wire-reinforced canvas ductwork to deliver conditioned air to the building and for air being returned to the temporary climate control equipment.
- Securely anchor temporary exterior ductwork to avoid wind damage.
- Interior distribution ductwork shall consist of polyethylene tubing (Layflat) of the appropriate diameter for equipment being used.
2.6 – Monitoring Devices
- Electronic monitoring devices shall be used 24 hours a day while temporary climate control equipment is in place, furnished to monitor and record dry bulb temperature and relative humidity in the space.
- Monitoring devices shall record readings in not greater than 15-minute intervals and be capable of downloading recorded data. Provide a device for every 10,000 square feet of floor space and at least one for each floor.
PART 3 – EXECUTION
3.1 – Preparation
- Coordinate layout and installation of temporary climate control equipment with finish trades.
- Modify and extend temporary dehumidification, heating, cooling, and ventilating as required by the progress of the finish work.
- Provide weather protection and environmental controls as required to prevent damage to the work, and to other property.
3.2 – Application of Temporary Dehumidification and/or Climate Control
- Configure temporary dehumidification and/or climate control equipment to maintain occupied space temperatures between 40°F and 80°F unless noted otherwise.
- Maintain relative humidity at or below 60% unless noted otherwise (recommendation is maximum of 20% RH for all concrete drying with a maximum 45% for general construction drying).
- Distribute air evenly to be free of drafts and dead spots and to maintain consistent conditions throughout the space. Suspend temporary system from the existing ceiling structure, where possible. Coordinate with the architect and other crafts for mounting locations within the building.
- Keep all building envelope doors closed and cover all openings to maintain a reasonably airtight envelope around the space to minimize infiltration of outside air and avoid pockets of high humidity.
- Maintain return air paths and the means for process air or reactivation air to escape, as required, for operation and to conform to specifications throughout the duration of this project.
- Dehumidification equipment will be used to control the environment in the space 24 hours a day while joint compounds, fireproofing, self-leveling sub floors, flooring, millwork, and finishes are being installed and until the materials in the space reach moisture levels as recommended by the manufacturer(s) until building is commissioned.
- Utilize temporary ducting and/or circulation fans to distribute the dehumidified air to all areas of the building requiring temporary dehumidification or climate control.
3.3 – Testing
- Utilize a sling psychrometer or digital hygrometer or remote monitoring device to measure dry and wet bulb temperatures in each affected space. Record readings at the beginning and end of each shift as a minimum, including outside ambient conditions.
- Deliver report to architect weekly.
3.4 – Removal of Temporary Facilities
- Maintain the temporary dehumidification and/or climate control system in service until building HVAC is commissioned.
- Completely remove temporary dehumidification and/or climate control equipment and all ancillary materials and accessories from the site at the successful commissioning of the permanent HVAC system.
3.5 – Cleaning
- Clean and repair damage caused by installation or use of temporary climate control equipment. Where disposal of spoil and waste products, whether or not they are contaminated, is required, make legal dispositions off-site following governing authorities’ requirement.
In my opinion, both specification sections should be included in your project documents. I hope this article helps our industry move toward responsible and safe construction practices and helps our trades include the necessary preparations and costs for these measures. Let me know if you have other recommended specifications or measures for our industry.
REFERENCES
- 2021 Fundamentals – Chapter 10 – Indoor Environmental Health
- 2021 Fundamentals – Chapters 25, 26 & 27 – Heat, Air, and Moisture Control in Building Assemblies
- 2000 SMACNA – Duct Cleanliness for New Construction Guidelines
- 2008 ANSI/SMACNA – IAQ Guidelines for Occupied Buildings Under Construction, 2nd edition
- 9/2002 ASHRAE Journal – Harriman, Schnell, & Fowler, “Preventing Mold by Keeping New Construction Dry”
- ASHRAE Guideline 10-2016 – Interactions Affecting the Achievement of Acceptable Indoor Environments
- “Green” guides in general
Chuck Dale-Derks, P.E.
Published April 13, 2022 in Engineered Systems Magazine
Chuck Dale-Derks, P.E., is a principal at McClure Engineering, a mechanical and electrical consulting engineering firm dedicated to the development of innovative solutions to unique engineering problems.