Storm (Tornado) Shelters for K-12 Schools — Considerations
Mechanical, electrical, plumbing, and fire protection design for storm shelters at a school facility require considerations outside the normal facility design parameters and thoughts.
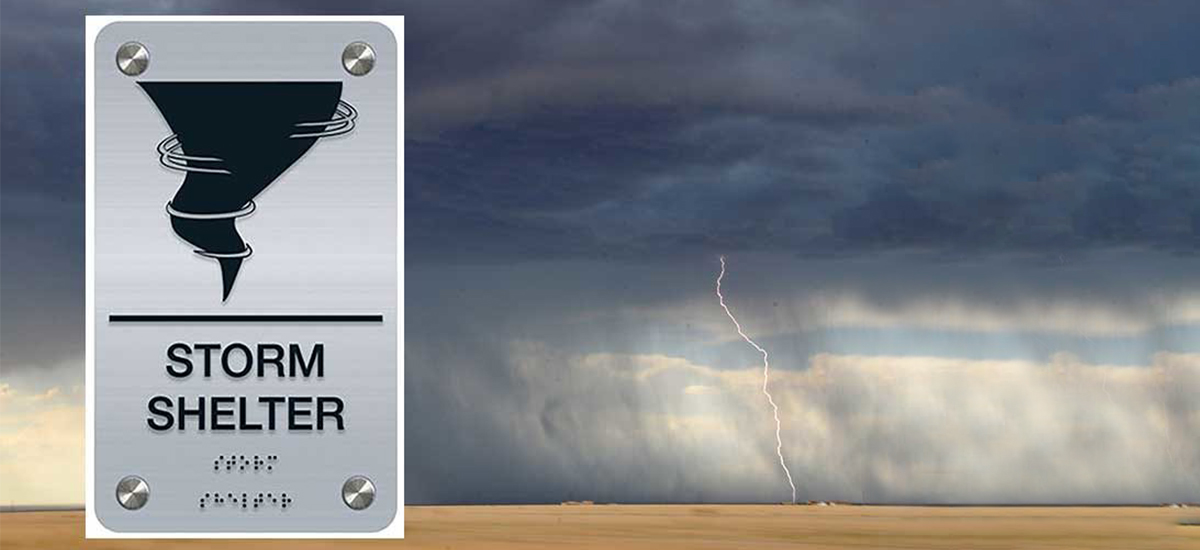
When making coffee at the office, can I lick my fingers to help separate the filters, like I do at home? No. I don’t believe my fellow employees would appreciate this approach. I must patiently and carefully separate the filters without licking my fingers to keep my fellow employees happy and healthy. Or should I even be using latex or vinyl gloves for an absolute best practices approach?
Storms and storm shelters aren’t new, but including storm shelters as part of education facility design and construction is new to our industry as our country, states, and/or municipalities adopt the latest building codes. Storm shelters are required at all 911 call stations; emergency operation centers; and fire, rescue, ambulance, and police stations as well as educational occupancies through grade 12 with occupant loads of 50 or greater. Some state codes, like Indiana’s, define “storm shelter,” “safe room,” and “best available tornado refuge area” as different entities. For the purpose of this article, I will only consider facilities designed to code, so the terms are not differentiated, and the design and construction of every facility should follow the code as best as it can be interpreted. So, are we designing these shelters correctly? Are we using best practices? Where do we find information on details of the MEP design?

Figure 1: Fire water service and fire department yard connection.
DESIGN CONSIDERATIONS
Like Winston Churchill famously said, “Let our advance worrying become advanced thinking and planning.”
The ‘burden’ of a storm shelter is shared among several partners or team members. Architects play a critical role in choosing the proper size and location for a storm shelter and specifying the proper door and window protection. The structural engineer must design for the demanding wind and impact loads and consider lay down, rollover, and collapse hazards. Mechanical, electrical, and plumbing engineers must provide a design that offers the proper ventilation and emergency backup resources. The construction trades must be held accountable for proper execution through quality assurance and inspections. The final burden and responsibility are in the hands of building owners to properly maintain the shelter, maintain the emergency operations plan, regularly renew the shelter disposable materials, and regularly practice and drill personnel on its use.

Figure 2: In-line ventilation fan and roof penetration prior to duct installation.
Mechanical, electrical, plumbing, and fire protection design for storm shelters at a school facility require consideration outside the normal facility design parameters and thoughts. ICC-500 requires protection for all openings larger than 3 1/2 square inches (2,258 mm2) in area for rectangular penetrations of 2 1/16 inches (52.38 mm) in diameter. This protection typically consists of ¼-inch thick (6.35 mm) steel plate shrouds or baffles surrounding all openings and penetrations.

Figure 3: In-line ventilation fan assembly installation served by emergency power.
Wind speeds in ICC-500 are much higher than wind speeds in ASCE-7 or the International Building Code. Hurricanes generate wind speeds from 74 mph (119.1 Km/h) to more than 150 mph (241.4 km/h), while tornadoes generate wind speeds to more than 250 mph (402 km/h). Designing for these conditions requires much thought and involves forces from all directions. Corresponding walls and roofs must withstand impact from a 15 pound (6.8 kg) wooden 2×4, propelled at 100 mph (161 km/h) and 67 mph (108 km/h), respectively. Design forces include requirements for tie-downs to the foundation and adequate foundation sizing to resist the design overturning and uplifting forces. Components used, including louvers, curbs, anchors, supports, etc., should be tested and rated for these wind and impact forces. Texas Tech University is no longer offering debris impact testing services for standards compliance. UL and Intertek offer testing of storm shelters and components, but I have not found listings or test results for MEP trade components. I am sure more components will be tested, and manufacturers will be advertising their compliance in the near future.

Figure 4: Half-inch steel barstock assembly to be mounted in the topping slab above the precast tees.
SHELTER DESIGN PUBLICATIONS TO REFERENCE
Here are a few publications to reference when designing storm shelters.
- The ICC 500-2014, “ICC/NSSA Standard for the Design and Construction of Storm Shelters,” is published jointly by the International Code Council and the National Storm Shelter Association.
- FEMA P-361, Third Edition, March 2015, “Safe Rooms for Tornadoes and Hurricanes, Guidance for Community and Residential Safe Rooms.”
- FEMA P-424, December 2010, “Design Guide for Improving School Safety in Earthquakes, Floods, and High Winds.”
- FEMA Comprehensive Preparedness Guide (CPG) 101, Version 2.0, November 2010, “Developing and Maintaining Emergency Operations Plans;”
- National Concrete Masonry Association TEK 05-14, “Concrete Masonry Tornado Safe Rooms;”
- NFPA 1616-2017, “Standard for Mass Evacuation, Sheltering, and Re-entry;”
- ASCE 7-2016, “Minimum Design Loads for Buildings and Other Structures.” Changes in the wind provisions from the 2010 edition to the 2016 edition significantly increased component and cladding pressures and changed roof loads for low-slope roofs. This is the referenced standard in the IBC-2018. The IBC-2015 and 2012 reference the 2010 version. If your municipality still enforces the 2009 IBC, then it references ASCE 7-2005. It’s a good practice to review the updates, consult with the local authorities having jurisdiction (AHJ), and possibly use the most recent version.
In my opinion, none of the publications provide clear fabrication, construction details, or guidance on how to properly and best protect roof-mounted MEP systems and MEP penetrations through the structure.

Figure 5: Structural design detail of 2” bar grating at opening below rooftop unit.
21 00 00 FIRE SUPPRESSION
In McClure Engineering’s first storm shelter design, we provided a single underground fire water service line with a post indicator valve routed to the building into the storm shelter equipment room, where it feeds two zones: one feeding the storm shelter and the other back below grade to the balance of the building – classroom and administrative areas. The system has a yard fire department connection in the front of the building that serves the entire building. Keeping penetrations below grade protects the lines from potential projectile damage. I recommend this single-service approach for any ground-up facility.
In designs that have been completed since we designed our first facility, and in storm shelter additions to existing buildings, a separate fire water service line is routed to the storm shelter. This fire protection system has its own post indicator valve on the water line and a separate yard fire department connection feeding into the system. It also has a separate exterior alarm bell and strobe. Signage is required to clearly indicate that the service serves only the storm shelter, and the main building must also be labeled to identify that it serves only the main building.
Placement of sprinkler heads also requires careful consideration. NFPA 13 allows the heads to be installed at the bottom of the structural precast tees or double tees. This placement could delay the activation as the heat must build down from the roof deck to release the head. Storm shelters include a perimeter wall that has a minimum fire-resistance rating of two hours.

Figure 6: This louver is not designed to prevent water penetration.
22 00 00 PLUMBING
Plumbing designs for a tornado storm shelter are much less demanding than hurricane shelters due to the difference in storm duration.
Rainwater is not addressed in a tornado storm shelter; however, in ICC 500, section 703.8, the rainfall rate for the primary roof drainage system for a hurricane shelter shall be determined by adding 3 inches (76.2 mm) of rainfall per hour to the rainfall rate established from the normal figure and project site. In St. Louis, some municipality ordinances and good design practice will use 6 inches per hour rainfall in lieu of the code minimum of 3.2 inches per hour. In ICC 500, section 703.8.2, the rainfall rate for the secondary (overflow) drainage systems shall be determined by adding 6 inches (152.4 mm) of rainfall per hour to the rainfall rate. It may be pertinent to consider this rainfall for a tornado shelter as well.
Fixture quantities are listed in ICC 500, so this is the easy part. Understanding the water supply and sanitary drainage requirements is another area open to interpretation. A hurricane shelter serving a community and designed for greater than 50 occupants requires 1 gallon per occupant for domestic water and 1.5 gallons per occupant for a sanitary system. In my opinion, an underground water and sanitary service is protected and adequate; however, storm flood levels and grade need to be considered for the volume of storm piping to a nearby manhole or to some point away from the building. I have not seen a recommendation for sanitary storage, or “valving,” as the code indicates, that allows appropriate storage. Thus, I don’t need to worry about this because my design facilities are in the Midwest and tornado shelters do not require this storage, right?

Figure 7: A close up view of the louver that is missing seam welding to seal the assembly.
23 00 00 HVAC
Air exhaust or intake openings that terminate outside of occupied shelter areas and occupant support require exterior wall and roof impact-protective systems. Ideally, these components would be tested and appropriately rated, but finding tested and rated components can be challenging for each scenario. The code and reference text are clearly applicable to doors and windows but could possibly be used for storm louvers. I’m just not certain how to test for fragmentation and penetration of small pieces and still allow a large volume of air in or out of the storm shelter.
ICC 500-2014, section 306.4, states, “Impact-protective systems shall be tested for missile impact in accordance with Chapter 8.” And, with exception, “Nonoperable, permanently affixed shields or cowlings are excluded from pressure testing requirements of Section 806.5.”
ICC 500-2014, section 306.6, covers anchorage of doors, windows, and shutters. It does not state requirements for roof curbs or louvers, but I think it’s clear that these, too, must follow these guidelines.
FEMA P-361 describes impact test pass/fail criteria and is based on not allowing the 2×4 missile impact to perforate the interior surface of the tested door nor allowing any part of the test specimen, including hardware, to become disengaged or dislodged. In addition, no pieces of the interior surface large enough to cause occupant injury can be propelled more than 5 inches into the room.
If you’re looking for products that meet the above criteria, you may need to search for “Windstorm-Rated Products” instead of using hurricane or tornado in your search.
Exhaust fans, air intake, and air relief hoods are frequently blown off their curbs because they are poorly attached. There is little information on the capability of a curb to hold down the equipment and what forces might be present with the equipment installed. I had a roof intake hood blown off a six-story building in St. Louis by a microburst of wind. The hood was large, roughly the size of a 747 wing section, and only anchored with four screws, one per side. The incident occurred overnight, so, fortunately, no one was injured; however, the hood did impact the security guard’s car, which was the only vehicle parked in the adjacent parking lot.
FEMA P-424, Table 6-1, describes requirements for anchoring roof-mounted equipment to curbs. It details quantity and placement of No. 12 screws (0.2160 or 27/125-inch basic diameter) for appropriately anchoring the equipment. The attachment of the curb to the roof also needs to be designed and specified.
It should be noted on drawings that assemblies shall be rated for FEMA P-361 (Shelter Missile) 15-pound, 2×4 lumber at an impact speed of 147 feet per second (100 mph) and momentum 68 lbf-s (pounds force per second), so, then, it’s up to the contractor to make sure it meets the requirement. He can easily do this, right? Engineers need to give clear direction on requirements for protection and anchoring.
For roof penetrations, we have used a detail of a rebar or ½-inch steel barstock assembly. However, most recent peer reviews have requested a rated assembly, so the use of a storm-rated louver mounted in the horizontal opening may be more appropriate. The barstock or rebar grid assembly will not stop small debris. A 2 ½-by-2 ½-inch barstock assembly is about 60% free area, so, per the Sheet Metal and Air Conditioning Contractors’ National Association (SMACNA) HVAC System Duct Design Guide, it imposes a total pressure drop that correlates to 0.97 times the velocity pressure of the airstream. An equivalent storm-rated louver with only 40% free area imposes a total pressure drop that correlates to about 3.0 times the velocity pressure of the airstream, which is a significant energy cost for the life of the facility.
Either design could allow rainwater into the building, but I know of no way to prevent this if the rooftop unit or hood is blown off the building. Too many “what ifs,” and I still need a means to get air in and out of the shelter.
Another recommendation is to use a concrete curb under the equipment support curb. This may be a good idea to keep roof storm water from flowing into an opening after the rooftop equipment is ripped off the roof but can be a challenge to construct. It requires rebar properly bent and set into place and may require a separate pour for the curb on top of the topping slab. Envirobeam makes an enviro-curb that may meet these requirements, but I have yet to install one.
I would recommend an indoor air-handling unit, but this requires space within an expensive storm enclosure. A vertical unit would minimize the space requirement. Economically, the AHU fan could be used for emergency ventilation rather than a separate in-line fan.
For wall louvers, our first shelter had a louver that was not designed to prevent water penetration. Yes, they recommended a projectile-rated assembly be installed in front of a louver that drains and prevents water penetration. I think louver manufacturers have improved their offerings.
ICC-500 allows two options to deal with atmospheric pressure change (APC). The first is to allow for enough free ventilation to account for the change. The amount of area required is extremely large at 1 square foot per 1,000 cubic feet of shelter space. The second option is to account for APC in the structural loads on the shelter envelope. Although this results in higher structural loads, it seems to be the approach that most design teams utilize. Coordinate the approach with your team members.

Figure 8: Natural gas service and an emergency generator inside a protected enclosure adjacent to the storm shelter.
PIPING
Gas lines, if present, should also be anchored to the roof. Preplanning with anchor bolts set into the topping slab will ensure the installation meets the stringent criteria for wind, debris, and impact resistance.
ICC 500-2014, states, “Penetrations of the shelter envelope by hazardous gas or liquid lines shall have automatic shutoffs to protect against leakage due to movement of the utility line. The threshold movements for shutoff shall be as defined by the codes and standards governing such utility lines.” This leaves much open to interpretation; however, I think a seismic gas valve meets this criteria. Usually, this valve is mounted above-grade on the exterior of the building, so maybe it should be in a protected enclosure.
26 00 00 ELECTRICAL
When routing conduit, our contractor asked to route the shelter lighting on top of the precast tees and inside the topping slab; however, the structural engineer did not allow this due to concerns of strength and topping slab integrity. Routing them indoors means the contractor is working on a lift; however, this keeps all of the conduit accessible and does not compromise the integrity of the roof assembly.
Another decision has been the fuel source for the emergency generator. It can be natural gas or gasoline/diesel-powered. Gasoline or diesel requires more maintenance and care for fuel treatment and fuel levels. This may be best discussed with the owner and the local AHJ.
The mechanical ventilation system, emergency communications, and lighting shall be connected to an emergency power system for a storm shelter.
Emergency lighting for a tornado storm shelter is required to provide an average of 1 foot-candle of illumination (11 lux) in occupied shelter areas, occupant support areas, required corridors, passageways, and means of egress. Generally, we are providing emergency power for normal lighting levels.
Emergency lighting for a hurricane storm shelter is required to provide an average of 1 foot-candle of illumination (11 lux) in occupied shelter areas, occupant support areas, required corridors, passageways, and means of egress, but, in addition, a standby lighting system is required to provide an average of 10 foot-candles illumination (110 lux) in occupied shelter areas, occupant support areas, required corridors, passageways, and means of egress.
27 00 00 COMMUNICATIONS
It is important to have a National Oceanic and Atmospheric Administration (NOAA) weather receiver (battery-powered, continually recharging) that is Weather Radio Specific Area Message Encoder (WRSAME)-equipped. All U.S. and newer Canadian stations transmit WRSAME codes a few seconds before the 1,050-Hz attention tone that allows more advanced receivers to respond only for certain warnings that carry a specific code for the local area. This receiver can be integrated into door hardware to automatically unlock doors in the warning stage for access to a community storm shelter.
28 00 00 Electronic Safety and Security must be closely coordinated with the door hardware. It may be integrated with the NOAA receiver as indicated above.
Developing and implementing a solid safe room operations plan is central to the effectiveness of the safe room or storm shelter. The population protected by the safe room during school hours includes the students, staff, and visitors. The population protected by the safe room outside of school hours is made up of the surrounding residents within a half mile radius of the safe room. The maximum occupancy of the facility during tornadic events is 739 people (example).

Figure 9: Wall or roof pipe penetration protection detail.
SAFE ROOM OPERATIONS PLAN EXAMPLE (SPECIFIC TO TORNADO)
When a tornado watch is issued for the county, the site coordinator will notify the district safety coordinator or superintendent that the area is under a tornado watch. The designated safe room area will be cleared if necessary and readied for student, staff, and visitor occupancy should a warning be issued. The intended secondary use of the safe room is a physical education classroom/gymnasium and meeting space, and it is not anticipated that much clearing will be required for the safe room to be prepared for occupancy.
When a tornado warning is issued (tornado sirens activated) by the county emergency management director, students will be evacuated from their classrooms and proceed to the safe room along the prescribed routes and as illustrated on posted floor plan evacuation route maps. Room evacuation route maps to the safe room shall be posted on the inside wall by the door of each classroom of the school buildings and distributed to each teacher.
The weather will be monitored by the field manager, and the safe room will remain occupied by students and staff until the severe weather has abated and the National Weather Service has cancelled the warnings and watches, or they have expired.
The safe room will only be available for student, staff, and visitor use during normal school hours and will only be open to the general public outside of school hours.
Make sure the site coordinator or other responsible party knows how to monitor and turn off water, electricity, and gas in the event the school is damaged.
It is the site coordinator’s responsibility to develop community education and training programs and to prepare and distribute newsletters to area residents regarding the availability of the safe room. A mailing list of those inside the protection zones should be developed in order to correspond with them and make sure they understand the valuable asset their community has.
The safe room information letters will state the protection zone boundaries and include copies of the protection zone map appropriate to the respective address it is being sent to. In addition, other pertinent information and brochures regarding hazardous weather safety tips and instructions relevant to the operations of the safe room will also be sent. The safe room protection zone map, letters, and special needs form regarding the operation of the tornado safe room are to be posted on the school’s website for the benefit of the general public as well as those in the protection zone.
The following must be kept within the safe room area:
Communication equipment (to be kept in the safe room office):
- One NOAA weather receiver (battery-powered, continually recharging)
- One AM-FM radio (wind-up/battery-powered)
- One cellphone (may not operate during a severe weather event inside the FEMA Safe Room)
- Two hard copies of the safe room operations plan
- An emergency call list that includes the
- Fire department/li>
- City or county police department
- City or county emergency management
- County emergency management office
Emergency equipment:
- Ten flashlights (with backup batteries)
- Two fire extinguishers
First-aid supplies (basic first-aid kits are required and must be kept in the safe room office):
- First-aid handbooks
- Non-prescription drugs (aspirin and non-aspirin pain relievers)
- Adhesive tape and bandages in assorted sizes
- Scissors
- Tweezers
- Safety pins in assorted sizes
- Non-latex gloves
- Antiseptic solutions
- Antibiotic ointments
- Waterless, alcohol-based hand sanitizer
- Instant heat packs and ice packs
Water: Water will be available from drinking fountains within the safe room. Bottled water is optional. Typically, bottled water manufacturers indicate a shelf life of one to two years.5
Other supplies (optional – items determined necessary by the committee): These items will be kept in the storage room.
- A package of disposable diapers
- A box of sanitary napkins, toilet paper, facial tissue, paper towels, and/or napkins
- Towels and moistened wipes
- Disinfectants and chlorine bleach
- Trash containers and liners
- Compressed air horn and/or megaphone
Emergency generator:
- An emergency backup, gas-powered generator will supply the safe room area with electrical service for a minimum of two hours
- The school’s buildings and grounds supervisor will be responsible for the routine maintenance and inspection of the generator. Monthly inspections will be performed to ensure the generator will be ready and functional in case of an emergency.
Debrief the safe room management team (site coordinator) Conduct an evaluation after a drill, exercise, or actual occurrence to determine the adequacy and effectiveness of the plan and the appropriateness of the response by the team members.
Journal recording of weather event (site coordinator):
- The date and time of event
- The reasons for safe room use
- The time the safe room was locked down and unlocked
- Any comments regarding the weather event and operation of the plan
AFTER THE TORNADO
Keep students assembled in an orderly manner; in a safe area away from broken glass, other sharp debris, and power lines; away from puddles containing power lines; and distanced from emergency traffic areas. While waiting for emergency personnel to arrive, carefully render aid to those who are injured. Keep everyone out of damaged parts of the school, as chunks of debris or even whole sections of an adjacent building may fall down. Ensure nobody is using matches or lighters in case leaking natural gas pipes or fuel tanks are nearby. It’s very important for authority figures to set a calm example for students at the disaster scene and reassure those who are shaken.
The International Code Council is in the process of updating the ICC-500 and hopes to complete the update for inclusion in the 2021 version for a complete set of codes. There is still time to comment, but the first round of public comment ended in December 2019. Get involved and comment if you can. Any improvement that clarifies the design recommendations for the architect, structural engineer, MEP engineer, and contractor will greatly benefit our industry.
Chuck Dale-Derks, P.E.
Published March 23, 2020 in Engineered Systems
Chuck Dale-Derks, P.E., is a principal at McClure Engineering, a mechanical and electrical consulting engineering firm dedicated to the development of innovative solutions to unique engineering problems.